P 10 P 7 8 9
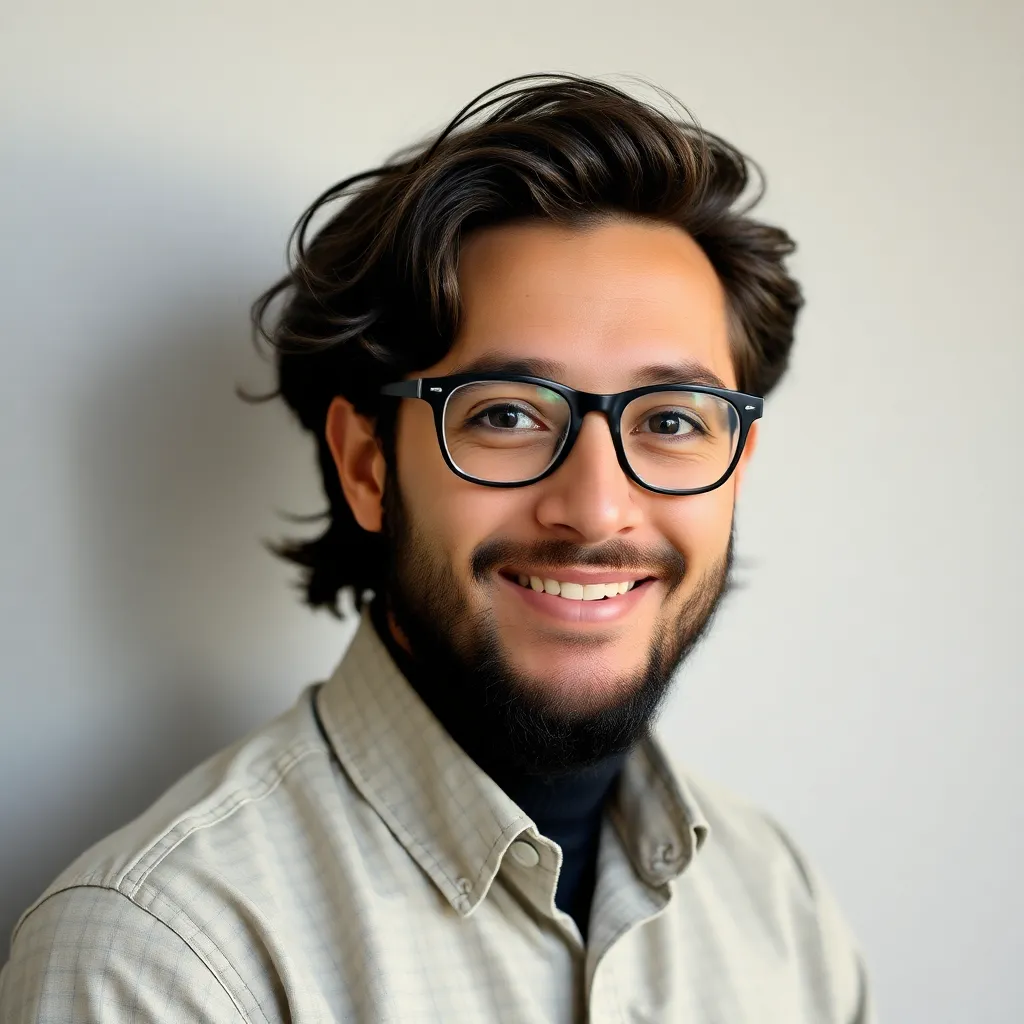
Greels
Apr 05, 2025 · 5 min read
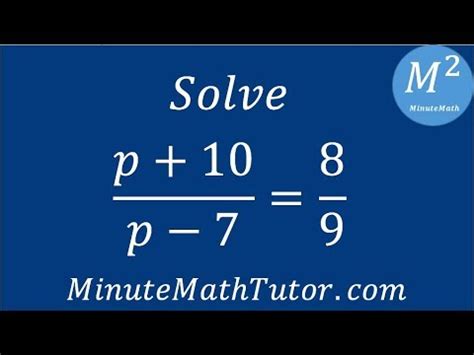
Table of Contents
Decoding the P10, P7, P8, and P9: A Deep Dive into the World of Precision Engineering
The designations P10, P7, P8, and P9 often appear in the context of precision engineering, particularly in industries requiring high tolerances and demanding specifications. While not standardized across all sectors, these labels generally refer to grades or classes of precision, indicating the level of accuracy and conformity to specific dimensions and surface finishes. Understanding these classifications is crucial for engineers, designers, and anyone involved in procuring or utilizing components requiring exceptional accuracy. This article will delve into the nuances of these designations, exploring their potential meanings, applications, and the critical factors influencing their interpretation.
Understanding the "P" Prefix: Precision and Beyond
The "P" prefix in these designations almost universally signifies precision. It suggests a component or process exceeding the tolerances found in standard manufacturing. However, the numeric suffix (10, 7, 8, 9) introduces a layer of complexity, as the specific meaning can vary depending on the industry and the specific standards being applied. There isn't a single universally accepted standard defining P10, P7, P8, and P9. Instead, these designations often emerge from internal company standards, industry best practices, or customer-specific requirements.
Potential Interpretations and Applications Across Industries
The interpretation of P10, P7, P8, and P9 often depends on the context. Let's explore some possibilities across various industries:
1. Surface Roughness (Ra): Micrometer Precision
In some contexts, these numbers might represent the average surface roughness (Ra) in micrometers. A lower number indicates a smoother surface. In this scenario:
- P10: Could signify a surface roughness of 10 µm or less, indicating a relatively rough surface. This might be suitable for less demanding applications.
- P7: Suggests a surface roughness of 7 µm or less, representing a smoother finish. This might be employed in applications where frictional forces need to be minimized.
- P8: Falls between P7 and P9, representing a moderate level of surface smoothness.
- P9: Indicates a very smooth surface, with a roughness of 9 µm or less. This is often necessary for high-precision components requiring minimal friction or superior sealing capabilities.
Important Note: The use of these designations for surface roughness is not standardized. Always refer to the specific documentation provided by the manufacturer or supplier.
2. Dimensional Tolerances: A Spectrum of Accuracy
In other instances, P10, P7, P8, and P9 might reflect dimensional tolerances. Here, a lower number typically indicates tighter tolerances, meaning less deviation from the specified dimensions.
- P10: Could indicate a wider tolerance range.
- P7, P8, P9: Would progressively indicate tighter tolerances, with P9 representing the highest level of dimensional accuracy.
Again, the exact meaning needs clarification from the relevant specifications.
3. Specific Internal Company Standards: The Need for Clarity
Many manufacturers employ their internal standards to define these designations. These standards might incorporate a combination of surface roughness, dimensional tolerances, material properties, and even testing procedures. It's crucial to obtain the detailed specifications from the company to understand the precise meaning in these situations.
4. Precision Machining Processes: Defining the Capabilities
These codes could also represent the capabilities of a specific precision machining process. For instance, a workshop might advertise its ability to produce components to P9 standards, implying a high level of accuracy achievable through their advanced equipment and expertise.
The Importance of Clear Communication and Documentation
The lack of universal standardization for P10, P7, P8, and P9 highlights the critical need for clear communication and comprehensive documentation. Anyone working with these designations must:
- Obtain Detailed Specifications: Never rely on the P-number alone. Always request and carefully review the complete specifications provided by the manufacturer or supplier.
- Understand the Context: The meaning of the designations heavily depends on the industry and application.
- Verify Measurement Methods: Clarify the methods used to measure and verify the specified tolerances and surface finishes.
- Use Consistent Terminology: Employ clear and unambiguous language when communicating these specifications to avoid misunderstandings.
Examples of Industries and Applications
The need for precision components characterized by P-numbers often arises in:
- Aerospace: Components for aircraft engines, avionics, and spacecraft require exceptionally tight tolerances and smooth surfaces to ensure functionality and safety.
- Medical Devices: Implants, surgical instruments, and other medical devices necessitate precision manufacturing to guarantee biocompatibility and performance.
- Semiconductor Manufacturing: The fabrication of microchips requires incredibly high precision at the microscopic level.
- Optics: Lenses, mirrors, and other optical components need exceptionally smooth surfaces and precise dimensions for optimal performance.
- Automotive: High-performance engine components and precision sensors often demand components meeting stringent tolerance specifications.
Beyond the P-Numbers: Other Factors Influencing Precision
While P-numbers might provide a general indication of precision, several other factors play a vital role in achieving and verifying the desired level of accuracy:
- Material Selection: The properties of the material significantly impact the final precision. Materials known for their dimensional stability and machinability are preferred.
- Manufacturing Processes: The choice of manufacturing process (e.g., CNC machining, grinding, polishing) drastically influences the achievable precision.
- Quality Control: Rigorous quality control measures, including regular inspections and testing, are essential to guarantee the desired level of precision.
- Environmental Factors: Temperature fluctuations and humidity can affect dimensional accuracy. Controlling the manufacturing environment is crucial.
- Calibration and Maintenance of Equipment: Precisely calibrated and well-maintained equipment is indispensable for producing high-precision components.
Conclusion: Navigating the World of Precision Engineering
The use of P10, P7, P8, and P9 as indicators of precision is a testament to the ongoing quest for ever-increasing accuracy in manufacturing. While the lack of universal standardization necessitates caution, understanding the potential interpretations and the importance of detailed specifications is paramount for engineers and professionals involved in this field. Always prioritize clear communication, comprehensive documentation, and rigorous quality control measures to ensure the successful production and utilization of high-precision components. Through careful consideration of all these factors, industries can achieve the levels of accuracy required for their critical applications, leading to improved performance, reliability, and safety. Remember, the pursuit of precision extends far beyond the simple numerical designation—it’s a commitment to excellence in every stage of the design and manufacturing process.
Latest Posts
Latest Posts
-
How Many Pounds Is 15 Grams
Apr 06, 2025
-
70 Millas Por Hora A Km H
Apr 06, 2025
-
18 Centimeters Equals How Many Inches
Apr 06, 2025
-
How Many Pounds Is 4 6 Kg
Apr 06, 2025
-
Cuanto Son 132 Libras En Kilos
Apr 06, 2025
Related Post
Thank you for visiting our website which covers about P 10 P 7 8 9 . We hope the information provided has been useful to you. Feel free to contact us if you have any questions or need further assistance. See you next time and don't miss to bookmark.